WEAVE
Children’s Center
Studio Summer 2022
Philadelphia, Pennsylvania, USA
Professor Matias del Campo
Director Ali Rahim
The 7ft tall model made entirely from 3d printed and laser cut pieces is a testament to the architectural capacities of our evolving technologies. This studio focused on the use of a robotic arm to print an architectural assembly via ceramic extrusion. The pieces were first designed as a part of a facade system and then modified to be printable geometries which would be strong enough to self support the ceramic assembly. Knowledge of ceramic manufacturing processes, clay material properties, Grasshopper and SubD modeling, and robotic programming were all essential to the mass production of the ceramic pieces. As an experienced ceramicist, I encouraged my team to take a more experimental route in the studio, which was to develop a way to rig the augur and extrusion canister in the robot’s end effector to print with pigmented clay. Clay pigment is a material used sparingly within the craft industry but largely overlooked in industrial ceramic production as it required the separate batch mixing of each pigment. However, in the scale of making thousands of pieces for a building, pigment allows for the pieces to be colored without having to individually glaze each piece according to a specific color profile. Through this method, the robot seemingly has a stake in the authorship of the design as the pigment is preloaded by a human, but is extruded according to how the augur processes the mixing of the differing densities of clay. For further experimentation, the process could be altered to include two end effectors (thus two canisters), one with pigmented clay and one with the white clay, with a designed head to conjoin the clay. The software which processes the robotic script can be altered to program when the clay is pressed out of each extruder in the print for further customization. This would also allow for a more intense marbling effect of the clay and the pigmented portions (see pieces below). The novel facade system of the ceramic pieces required a system structurally capable of holding the load as well as easily modified to accommodate adjustments in the shape’s geometry. The design for the project includes a core which supports a large truss system which holds the diagrid cage that locks into the floors. The diagrid’s geometry modifies throughout the project to hide behind the ceramic pieces as their form changes to accommodate different programs and allow more light into adjacent spaces. This was done through the careful scripting of the SubD geometries of the ceramic pieces to a point based grasshopper script.
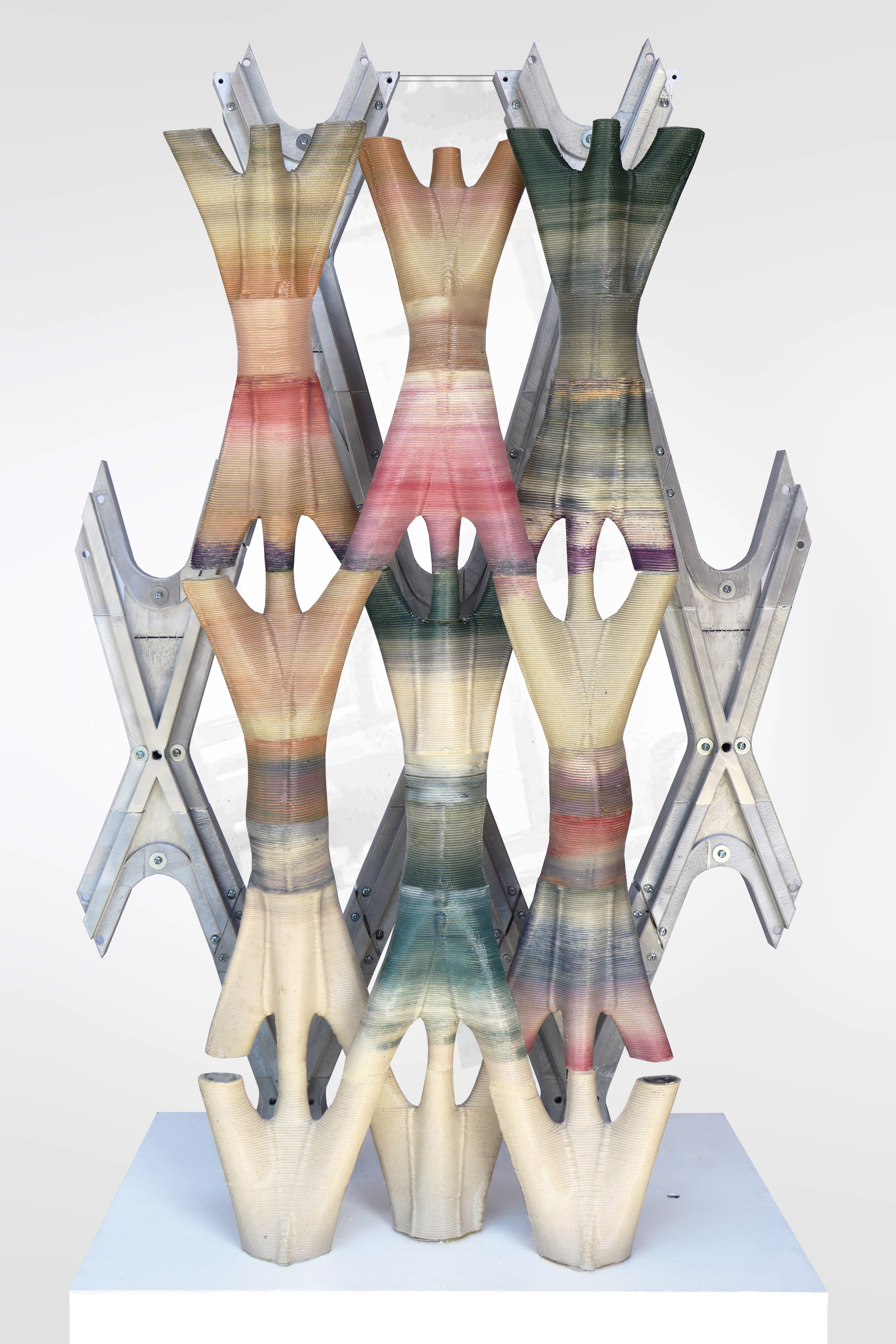
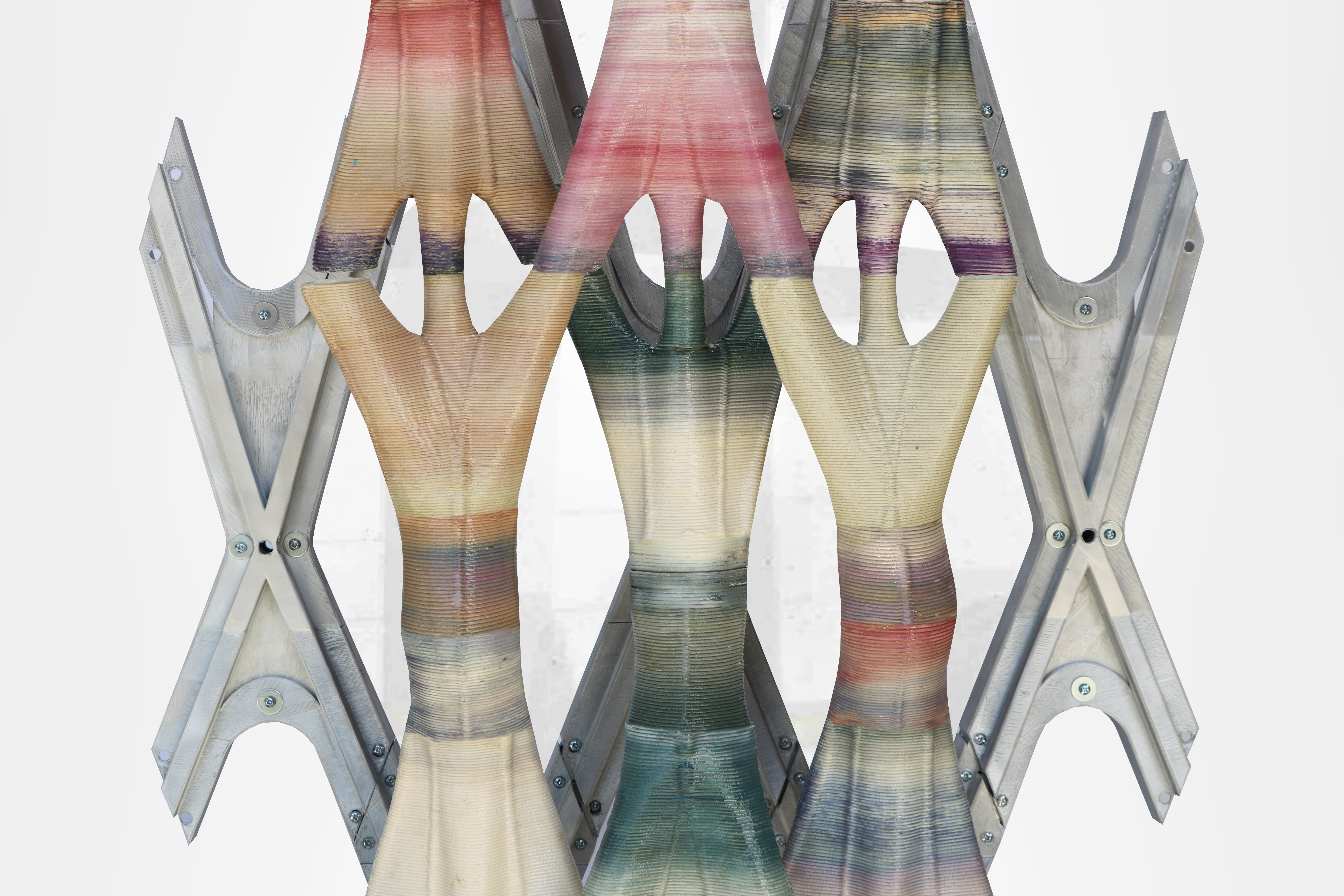
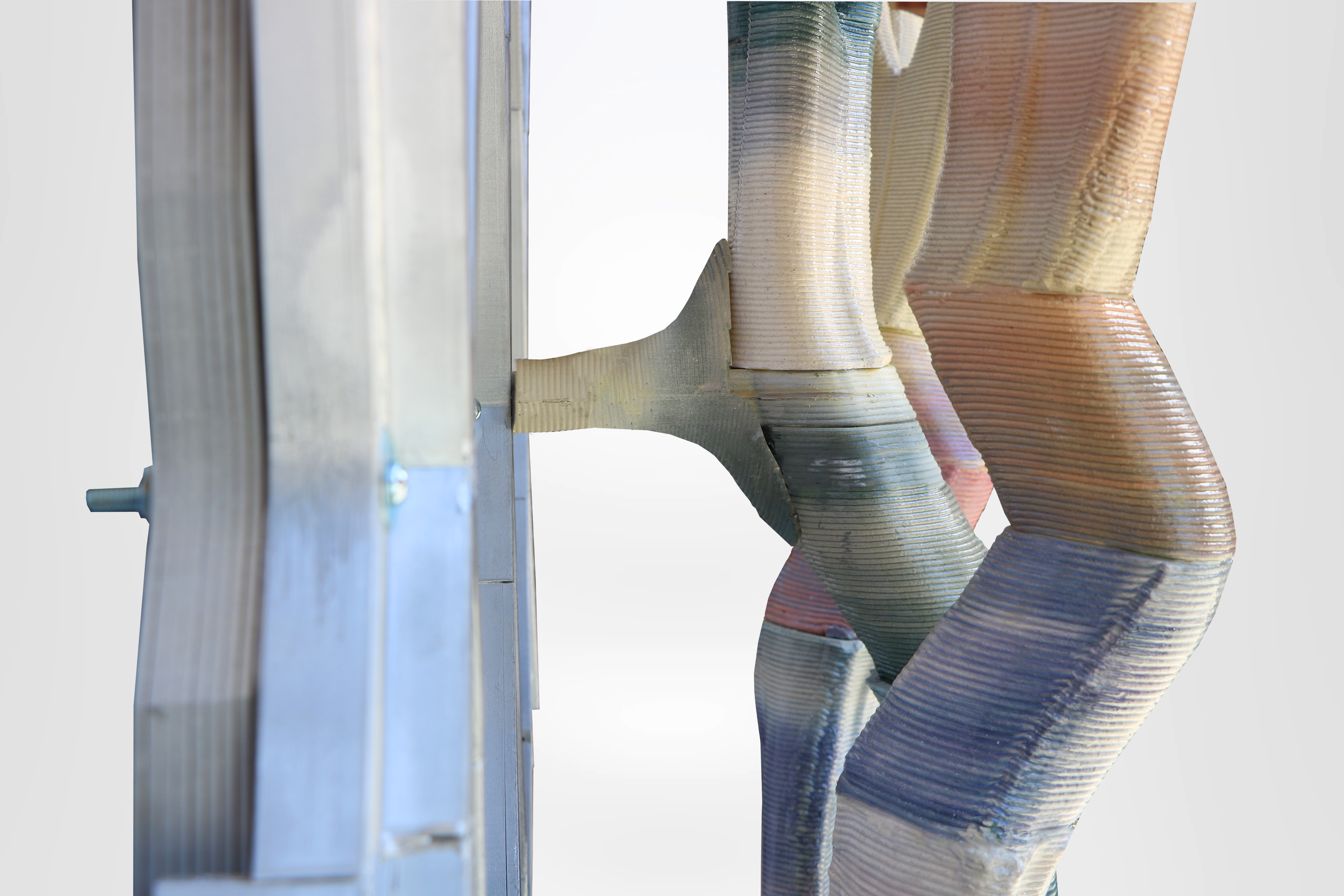
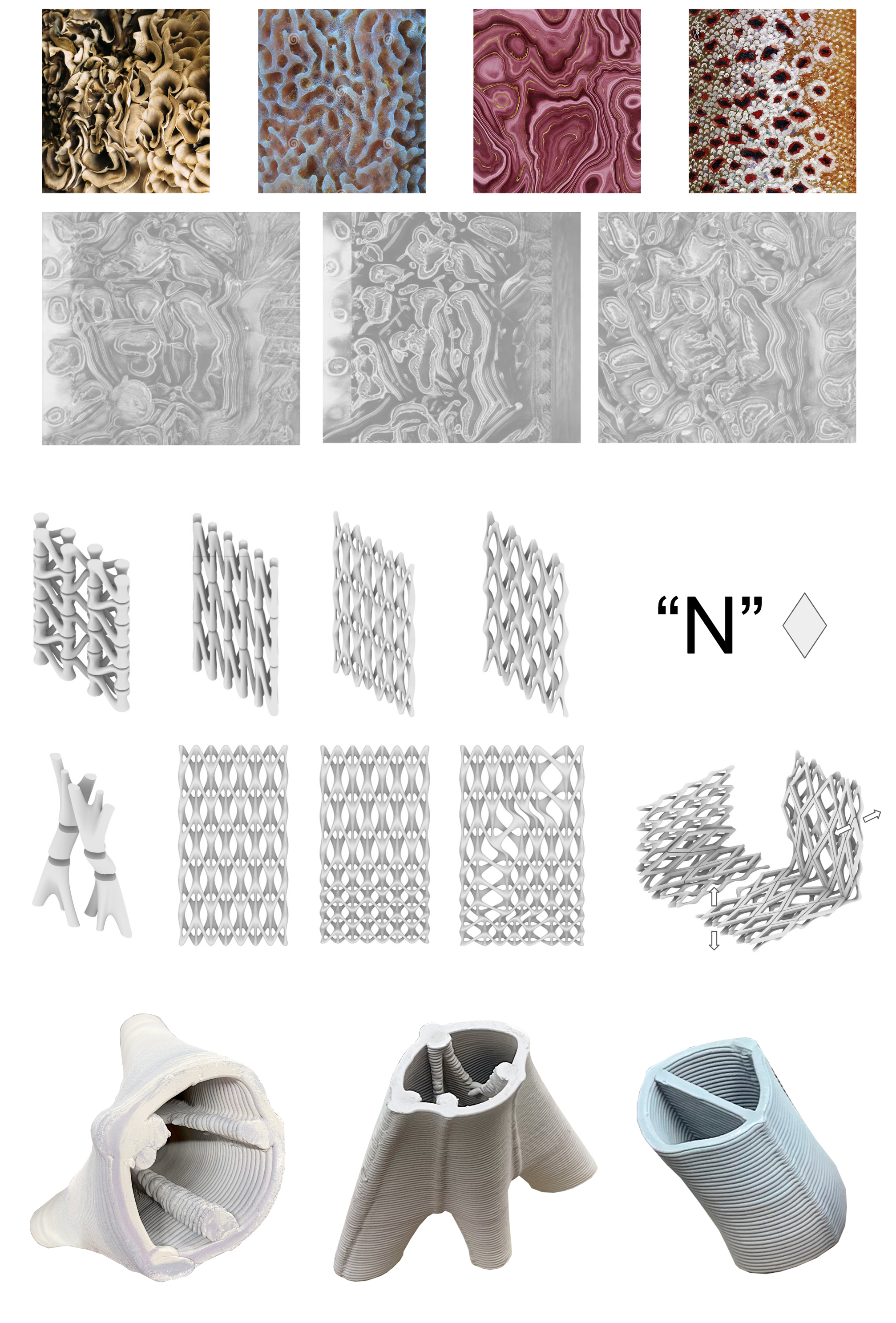
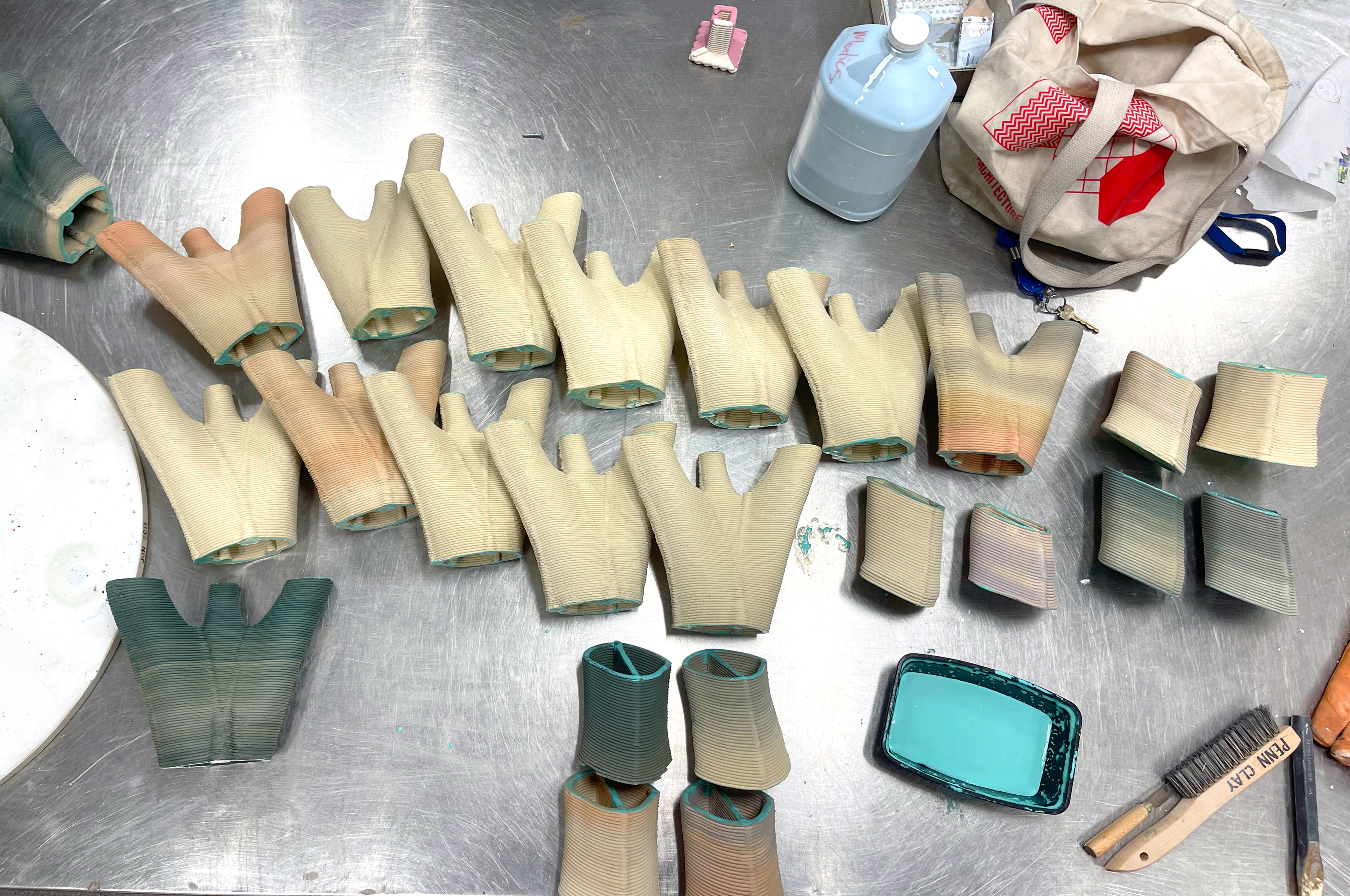
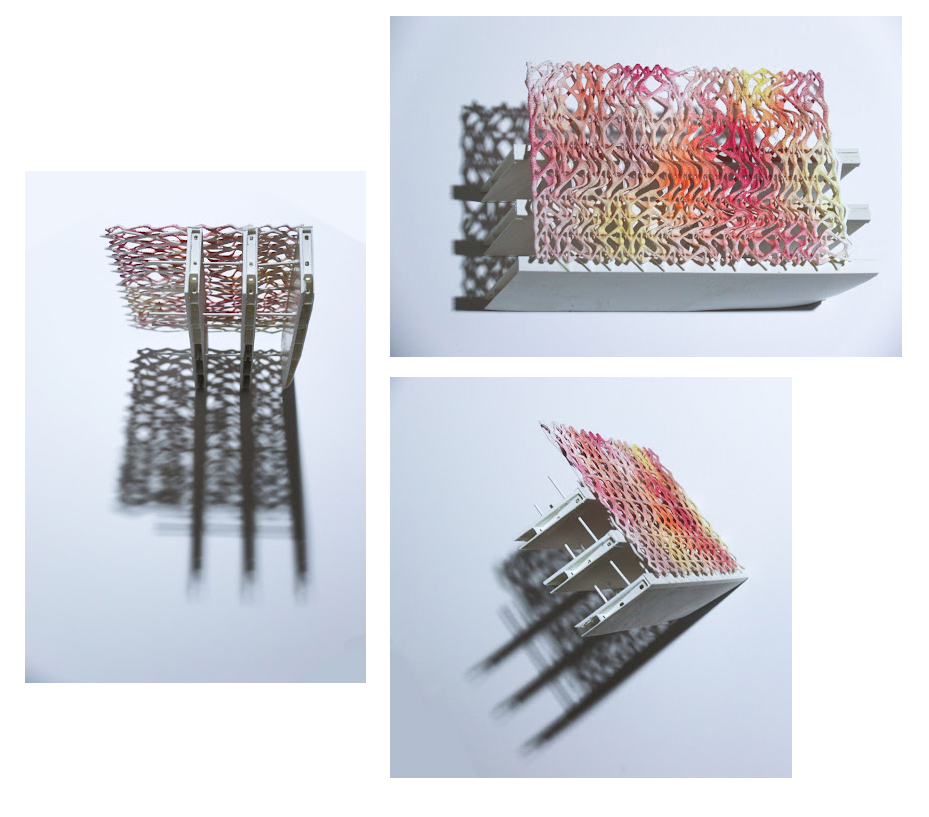
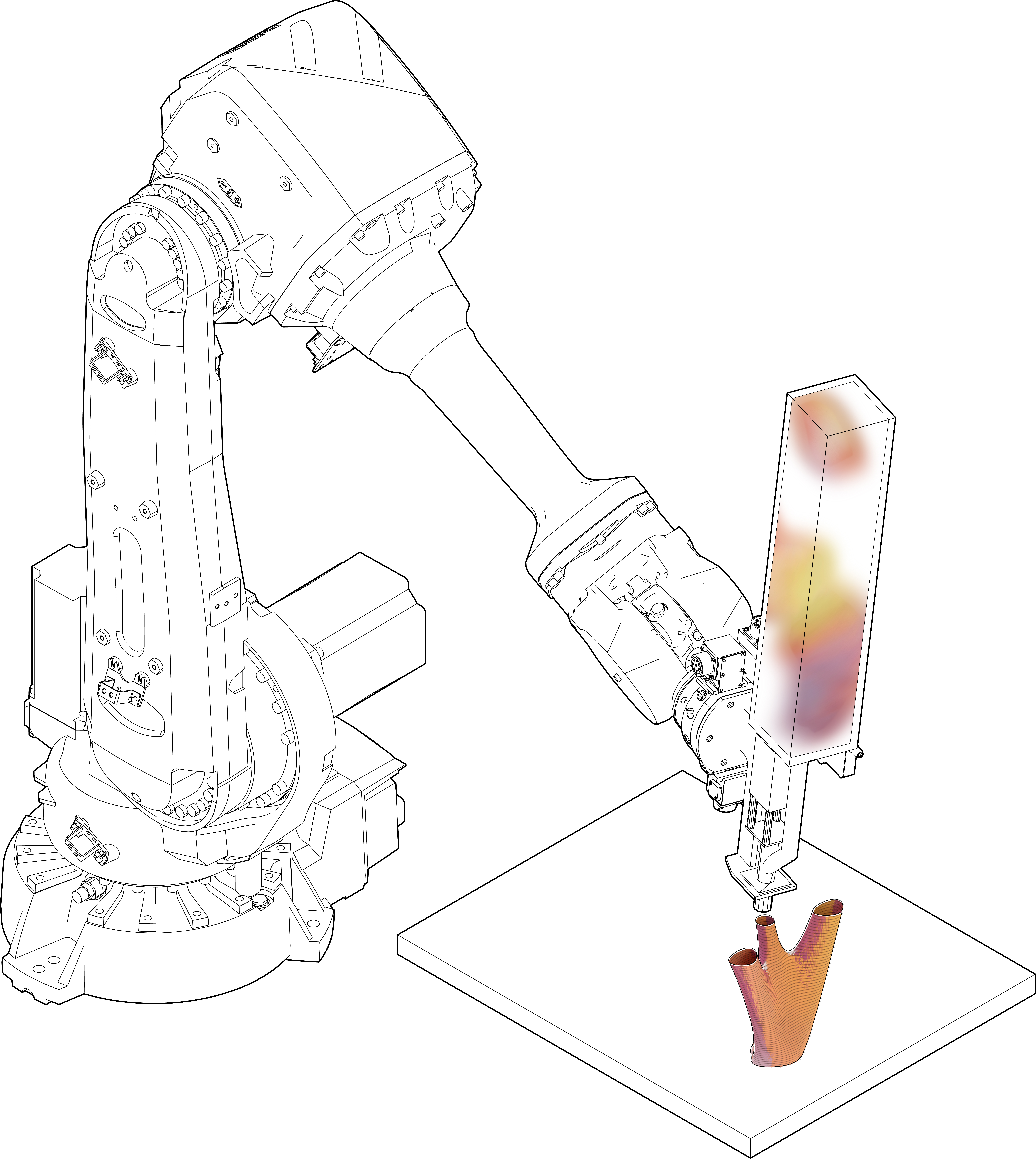
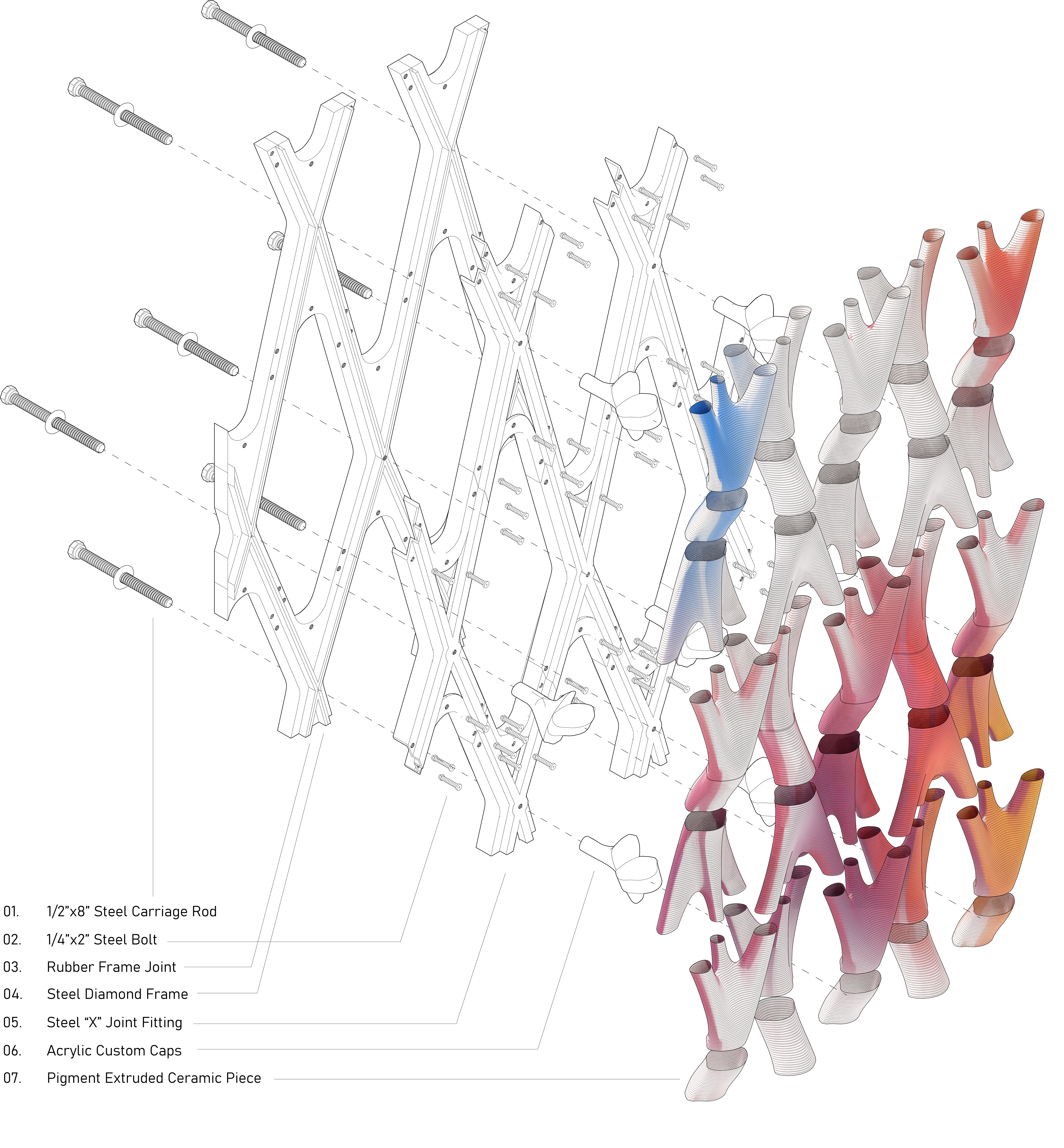

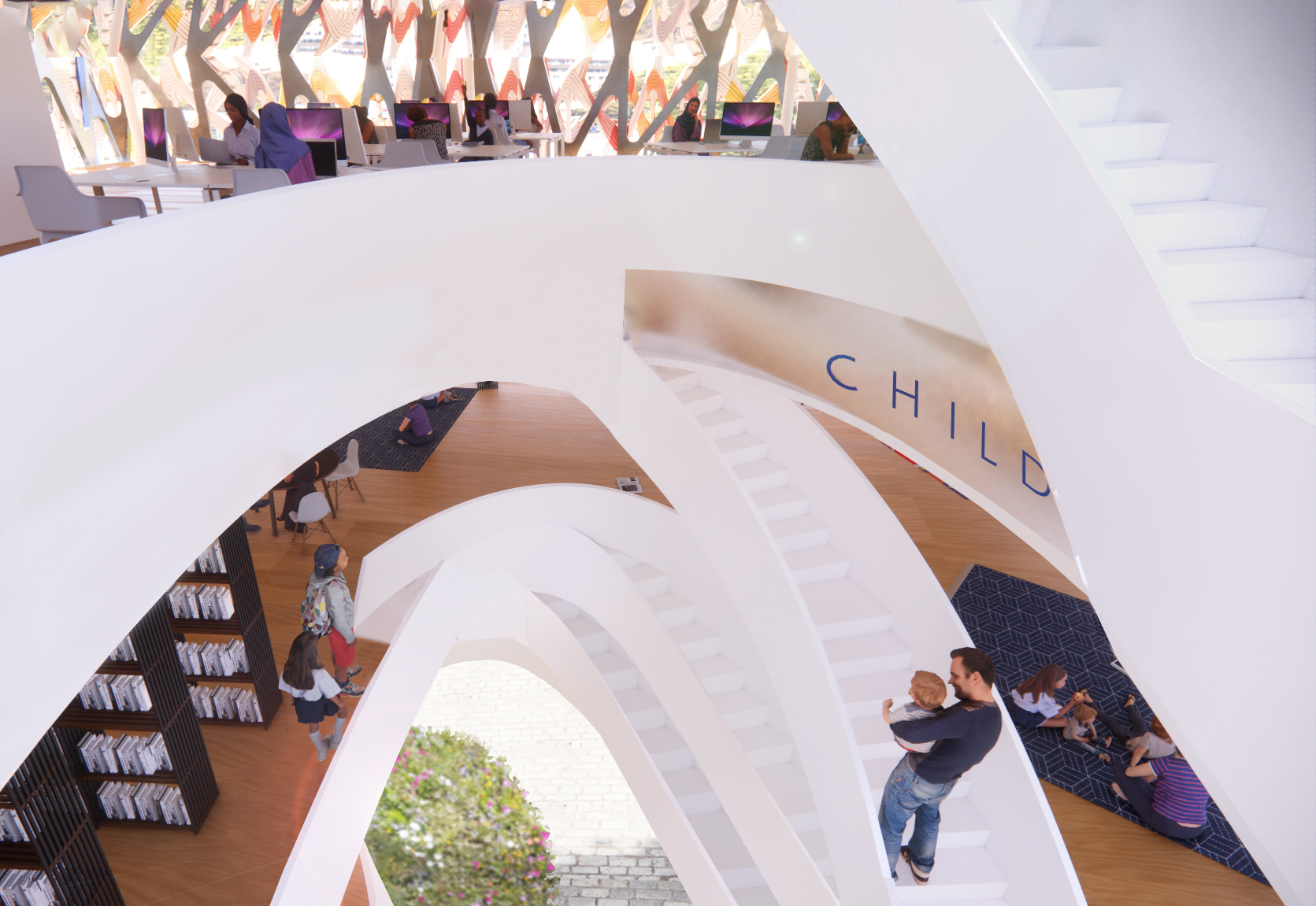
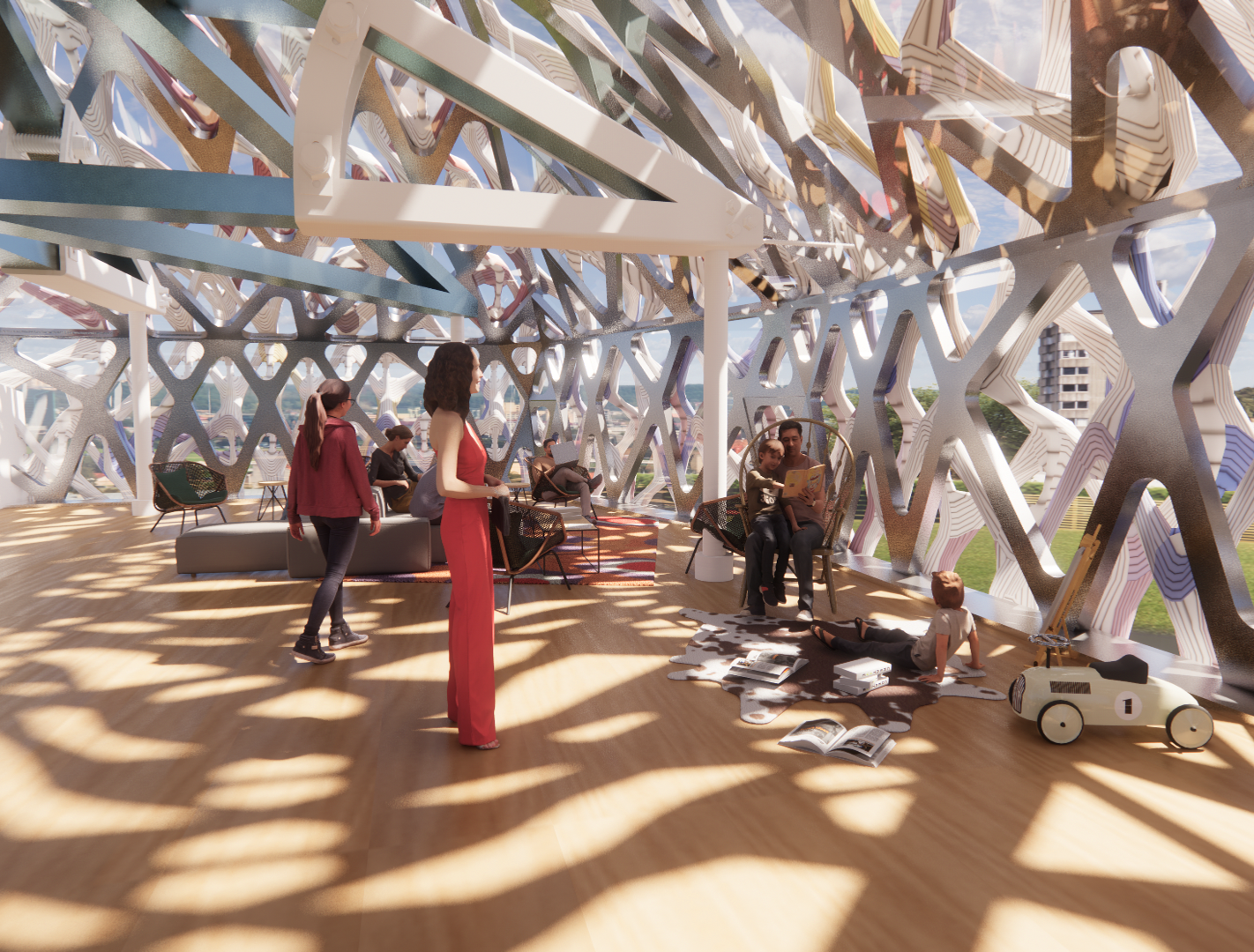